DDMRP与MRP:在不改善预测的情况下改善服务
即使没有需求变化,也无法执行生产计划。
任何有生产经验的规划者都知道,需求变化并不是造成扭曲的唯一原因。供应商、员工和设备也会让您失望。
通常,这种类型的变化被称为操作变化。下面的图表显示了虚构的“产品A”的BOM和路线。为了简化示例,我们假设每个购买的SKU都有 95%的时间都可以用于生产。在其他5%的时间里,供应商迟到了或者有质量问题,或者发生了其他事情,使其无法使用。同样,让我们假设每个资源都是95%可靠的。
现在,让我们计算两种原材料同时可用于1号设备进行加工的可能性。这是0.95 x 0.95 x 0.95(记住,1号设备的可靠性也只有95%),相当于0.86%。由于我们总共有五种原材料和五个连续的设备需要加工,车间能够按时生产出质量良好的产品A的总体可能性约为0.95^10,即约60%。
此外,与任何公司一样,我们虚构的车间有不止一个SKU,其有限的时间、资源和材料可以生产。为了有效地做到这一点,该公司使用了主生产时间表(MPS)。在下面的第二张图表中,您将看到八天的MPS样本,包括第一天产品A的发布。
我们刚刚审查了一些材料,工作中心需要按时提供合适的数量,才能完美地完成工作。在我们的例子中,成功的几率大约是60%。让我们假设每天成功执行时间表的几率是相同的,等于60%。那么,连续两天一切按计划进行的可能性有多大?0.6*0.6=36%。不难恢复计算,并理解连续8天(0.6^8)一切按计划进行的可能性小于2%。
DDMRP有什么不同?
缓冲区可以缓解变异性并消除牛鞭效应。
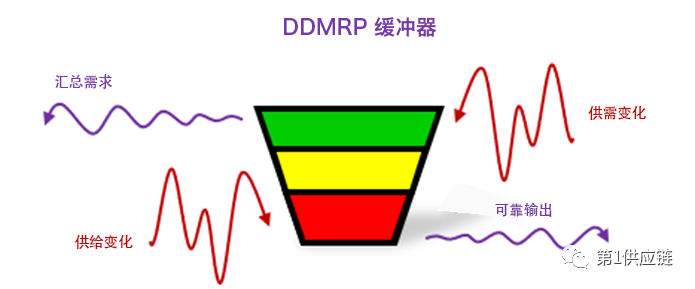
红区是嵌入缓冲区的安全区。红区的工作是确保可靠的产出,换句话说,为我们的客户提供高服务水平,并防止供需变化。
绿区的工作是汇总需求变异性,并在供应链的更远处提供相对统一的订单。
不需要冗长、详细、冻结的生产时间表。
DDMRP缓冲区的工作是通过在供应链层之间和BOM结构内部的关键点上创建与存储材料、时间和容量的独立点来解耦依赖性。以下数字比较了MRP和DDMRP视图。
在这里,我们看到相同的产品,A和B,具有相同的BOM和设备路由路径。但操作方法不同。在MRP世界中,我们需要至少提前30天安排产品A,并等待所有依赖和后续操作按时完成,没有错误或延迟。那个假设有多可靠?
由于DDMRP缓冲区在BOM结构中创建了存储材料、时间和容量的独立点,这使得产品A的交货时间缩短为14天和一次操作,产品B的交货时间为5天和一次操作。如果交货时间缩短,就没有必要长时间的时间表冻结。正如我们之前提到的,产品A的一切都按计划进行的可能性约为60%。
在DDMRP中,要生产产品A,我们只需要完成第4号操作,因为之前操作的结果已经存储在缓冲区中。更重要的是,我们只需要依靠一次最终操作,可靠性为95%,在MRP中比60%更一致。
同样的逻辑也适用于产品B。交货时间从14天压缩到5天,计划可靠性从70%(0.95^7,因为7个依赖项,每个依赖项的可靠性为95%)提高到95%(一次最终操作)。方法的巨大变化使这些新结果成为可能。
我们可以降低库存并改善服务,而不会提高预测准确性。
降低库存水平和提高服务水平的唯一方法是提高预测准确性。这个想法在行业中根深蒂固,知道精确的预测是不可能实现的,他们会把剩下的时间花在寻找完美的平衡上。忽略简单的事实,预测的准确性是不可能实现的,而且由于MRP的依赖性,完美的时间表也无法执行。
DDMRP缩短交货时间和提高适应性的能力使我们能够存储更少的库存,更有效地应对需求或供应波动而不妥协。如果需求发生变化,规划优先级发生变化,我们将构建市场所需的产品。最大的区别是,我们可以适应市场变化,因为我们储存了时间、材料和容量,或者仅仅因为我们有一个DDMRP缓冲区。我们不需要再生活在一个完美的世界里,让规划系统发挥作用。我们不需要提前30天详细了解市场需求,希望我们所有的供应商和车间运营都能完美运作,使我们的时间表能够执行。这就是设计缓冲区的原因。
我们只建造市场想要的东西。
对于计划,DDMRP使用实际的销售订单。因此,生产计划员可能是公司中第一个看到并对订单激增做出反应的人,并分配车间作业来满足需求。销售部门不需要打电话给计划人员,要求更改时间表,因为没有时间表。没有必要要求根据市场需求进行调整,因为生产是由需求驱动的。它以方法论的名义,需求驱动MRP。
DDMRP是一种库存管理方法,因为它可以适应不断变化和不可预测的环境。同时,它对用户来说更高效、更直观。它使我们能够打破一个闭环,在这个闭环中,增加服务和降低库存的唯一方法就是改进预测。但预测无法改善——特别是在不确定性和波动性增加的情况下。DDMRP为车间运营带来稳定性和可见性,让您的客户满意,为仓库和财务部门带来低库存。总体而言,高服务意味着您和您的客户都满意。